Интерес к самодельным компонентам вызван
тем, что при создании качественной автомобильной установки обойтись только
готовыми изделиями практически невозможно. В последние годы в
радиолюбительской литературе появилось немало публикаций, посвященных
самостоятельному изготовлению автомобильной аудиотехники, главным образом
усилителей. Но источник сигнала и усилитель -
только надводная часть целого айсберга проблем, встающих перед создателем
автомобильной установки. Огромное влияние на качество звучания оказывает
конструкция акустической системы, причем это влияние намного больше, чем в
"домашних" системах. Однако этот факт еще не стал очевидным и многие
автолюбители пытаются улучшить качество звучания простой заменой динамиков
и магнитол, хотя проблема вовсе не в этом.
Скептическое отношение к Hi-Fi в автомобиле
вызвано прежде всего безграмотным подходом к установке акустических
систем. Самая распространённая ошибка - установка мощных и
высококачественных динамиков на задней полке, а спереди - что придется,
или вообще ничего. Видимо, владелец на концерте предпочитает сидеть спиной
к сцене... К сожалению, радиолюбители только
недавно стали уделять внимание созданию высококачественных акустических
систем для автомобиля. Основная проблема - воспроизведение низкочастотной
части звукового диапазона. Далее приводится описание очень удачной
конструкции низкочастотной акустической системы для размещения под
передними сиденьями ВАЗ-2108 и 2109. Подобные методы можно использовать
для создания акустических систем в автомобилях других марок. В конструкции
использованы доступные и недорогие материалы.
Попытки получить достойные "басы" в салоне
автомобиля предпринимались с момента зарождения автозвука. До наступления
"эры сабвуферов" для размещения басовых динамиков использовалась задняя
полка. Несколько позже, когда до сознания масс дошло, что звук должен
исходить спереди, стали использовать передние двери, штатные места в
торпедо, кикпанели. И тут начались проблемы. Основное условие
качественного звучания – создание оптимального акустического оформления
для конкретных динамических головок. Для воспроизведения низкочастотного
диапазона необходимо выдержать оптимальный объем корпуса. При его
уменьшении относительно оптимума воспроизведение низких частот будет
ослаблено. От увеличения объема пользы еще меньше – колебания диффузора не
будут демпфированы в нужной степени. В результате воспроизведение низших
частот будет сопровождаться гулким призвуком, а при некоторой
"настойчивости" можно оборвать подвес диффузора или выводы звуковой
катушки даже при скромной подводимой мощности. Кикпанели и торпедо для
низкочастотного оформления обычно непригодны. Поэтому при построении
многополосных систем в автомобиле головки чаще всего располагают в
передних дверях. Во многих случаях это оправдано, так как большинство
автомобильных головок рассчитано именно на такое акустическое оформление.
Однако установка в двери имеет ряд недостатков. Трудно обеспечить
требуемый объем для головок, предназначенных для установки в такие виды
акустического оформления, как закрытый ящик или фазоинвертор, добиться
герметичности еще сложнее. Необходимо провести тщательное
вибродемпфирование и шумоизоляцию панелей и механизмов двери, иначе она
будет "подпевать" уже на средней громкости. Да и динамики нужны
влагостойкие. Альтернативный вариант, лишенный
этих недостатков – акустические системы под передними сидениями. Идея не
новая, двух–, трех- и даже четырехполосные автомобильные акустические
системы "почти как дома" были очень популярны в первой половине
восьмидесятых. В пору расцвета это были добротные изделия – с жесткими
корпусами, хорошими разделительными фильтрами и продуманным креплением.
Готовые корпусные колонки неплохо вписывались в интерьер автомобиля и
устанавливались без проблем. Довольно быстро они "ушли" с задней полки и
заняли место под передними сиденьями, где уже не так бросались в глаза
недоброжелателям. Между делом обнаружилось, что звучание от "переезда"
только выиграло. Но как только производители автомобилей уделили внимание
штатным местам, позиции корпусной акустики пошатнулись, а с появлением
сабвуферов она и вовсе сошла со сцены. Тонкостенные коробочки с крошечными
динамиками, появляющиеся иногда в продаже – всего лишь тень былой роскоши.
Диалектика учит нас, что развитие идет по спирали. Поэтому возобновление
интереса к акустическим системам под передними сидениями закономерно – это
позволяет относительно простыми средствами решить проблему "переднего
баса". Идея использовать ящики под сидениями как вариант акустического
оформления низкочастотного звена в многополосной системе была навеяна
действующими образцами в автомобилях ВАЗ-2107 и "Москвич-2141".
Воспроизведение частот от 40 – 50 Гц и звуковое давление этих систем
произвели сильное впечатление. Размещение ящиков под сидениями поначалу
казалось делом несложным. Но, заглянув в то место салона "зубилы", где в
дальнейшем предстояло стоять ящикам, я был немного ошарашен. Это была не
"классика", с которой произошло первое знакомство. Установленные мной для
себя требования "технического задания" состояли из трех пунктов: выжать
максимально возможный объем, не нарушить функциональность сидений,
обеспечить легкость монтажа (правда не в смысле облегчения демонтажа
злоумышленнику). Идея установки динамика показана на рис. 1.
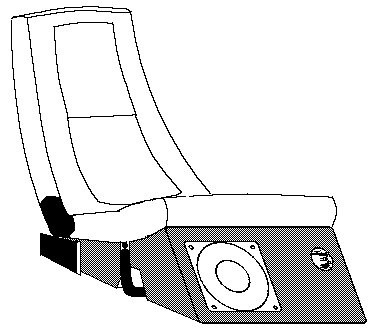 Рис. 1. Установка динамика под сидением
автомобиля.
Каждый, заглянувший под сидение, видел,
какой небольшой проем образован дугой передней опоры и каркасом. Поэтому
решение заключалось в том, чтобы сделать переднюю опору разборной. Для
этого было снято сидение, затем срублены заклепки, которые соединяют дугу
с каркасом. По размерам этих заклепок изготовлены болты (рис. 2), все
шейки которых взяты с заклепок. Только на конце резьба добавилась.
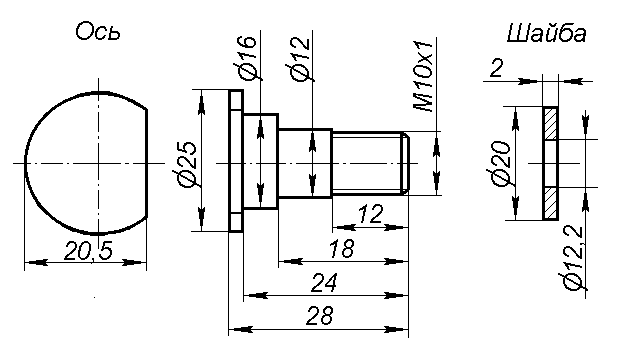 Рис. 2. Конструкция крепежных болтов.
Это хозяйство облегчило в дальнейшем
проектирование ящика. Скажу сразу, все проектировалось на месте, без каких
либо предварительных промеров, только путем проведения постоянных
прикидок. Для этого понадобился гофрокартон, ножницы и скотч.
Предварительно сидение было установлено на 4 болта салазок и откинуто к
подушке заднего сидения. Дуга передней опоры с пружинами тоже была
прикручена к полу, как положено. Болты, соединяющие все части сидения в
одно целое, лежали рядом. Из картона я вырезал полосу такой ширины, чтобы
она с минимальными зазорами разместилась между стойками дуги. Затем выгнул
профиль, с минимальными зазорами огибающий крепления дуги. Потом уже
подобрал приблизительно длины передней (до крепления) и задней частей
ящика. Следующим шагом было изготовление
боковых стенок. Это не составило особого труда, я просто опускал сидение,
смотрел, поднимал, подрезал лишнее и снова опускал. Самым быстрым способом
соединения частей макета я посчитал соединение с использованием скотча.
Потом была сделана верхняя часть макета. Сидение опущено, собранно на
болты, и вот вроде результат. Есть все необходимые размеры. Но как я тогда
ошибался! По снятым размерам из 12-
миллиметровой фанеры были изготовлены все части будущего ящика, за
исключением фрагмента, огибающего крепление передней опоры. Этот фрагмент
был изготовлен по композитной технологии. Стеклоткань по торцам боковых
сторон и дна ящика была подклеена, а затем пропитана эпоксидной смолой и
упрочнена еще несколькими слоями кусочков стеклоткани.
Когда все было собрано, пришло первое
разочарование. Ящик уместился на своем месте прекрасно, но вот сидение
вставать не хотело. Анализ показал, что промахнулся я с размерами боковых
стенок и с использованием в качестве материала для макета гофрокартона.
Каркас сидения имеет выгнутый профиль. При "примерках" он прогибал
гофрокартон. А так как для того чтобы прогнуть его, особых усилий не
требовалось, я этот подвох не заметил.
Лимитирующей позицией пока оставалась высота
боковых стенок. Постепенно уменьшая ее и проводя постоянные прикидки, я
добился максимального использования пространства. Хочу добавить, что я
прикидывал взаимное расположение ящика и сидения, передвигая последнее из
одного крайнего положения в другое. На этом этапе, возможно, придется
уменьшить длину задней части, если вдруг в ящик начнет упираться пруток
фиксатора промежуточных положений сидения.
Теперь ограничением стала выступать верхняя
часть ящика. При использовании фанеры я опять натыкался на то, что
выпуклая часть каркаса сидения упиралась в фанеру. Снижать высоту - значит
уменьшать объем ящика, который по прикидкам получался около 8 литров.
Опять проанализировав ситуацию, пришел к тому, что верх надо изготавливать
также по композитной технологии. При очередной прикидке объекта "на
местности", замерил расстояние от выпуклой части каркаса сидения до
боковых стенок ящика. Потом на чуть меньшем расстоянии от боковых стенок в
ящике были установлены дополнительные перегородки, расположенные под
небольшим углом к боковым и имеющие меньшую высоту, так что при очередных
прикидках расстояние между каркасом сидения и ребрами было порядка 10 мм.
Для них предназначалась роль не только ребер жесткости, но и линий
преломления стеклоткани при формировании верха ящика. От боковых стенок
стеклоткань резко спадала вниз до ребер. А между ними имела небольшой,
специально созданный прогиб. Ребра расположились только до изгиба нижней
плоскости ящика (рис. 3).
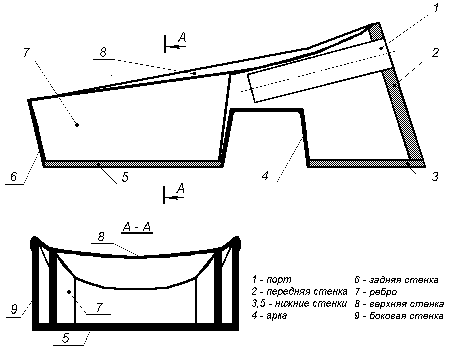 Рис. 3. Конструкция корпуса.
Дальше ткань просто равномерно натянул.
Перед пропиткой эпоксидной смолой можно провести еще одну прикидку. Я от
нее отказался, так был полностью уверен в успехе. Фронтальный срез ящика я
укрепил рамкой из брусков. К верхнему бруску была приклеена стеклоткань.
Затем жесткость верхней панели была доведена до приемлемой путем
наклеивания еще нескольких слоев стеклоткани. Причем последующие слои были
сделаны с напуском на боковые стороны и приклеены к боковым стенкам под
грузом. Замечу, что задняя, совсем узкая стенка была выклеена заодно с
верхней. После того, как просохла смола, я произвел вибродемпфирование
путем наклеивания визомата на поверхность фанеры. Стеклотканевую
поверхность вибродемпфировал резинобитумной мастикой.
Осталось изготовить фронтальную панель, на
которой должна будет разместиться головка. Я изготовил ее из двух слоев
фанеры, склеенных клеем ПВА и дополнительно стянутых шурупами. Отверстие
под головку вырезал на токарном станке. Как я раньше упоминал, в первом
варианте решил использовать 6-дюймовые мидбасы. По периметру панели снял
фаску достаточно больших размеров. Потом, приложив панель к ящику,
приклеил ее, заполнив полость, образованную торцами стенок ящика и фаской
панели, смесью мелких опилок и клея ПВА. Прочность получилась достаточной,
так как при переходе к второму варианту пришлось потрудиться стамеской,
расшивая проклеенные поверхности. Что же в
итоге получилось? Ящик при определенной сноровке устанавливается минут за
пятнадцать. Основная проблема - на ощупь завести болты соединения передней
опоры и сидения. Я был готов потратить на это дело и час, так как
устанавливаются ящики один раз и надолго. Встают достаточно плотно.
Никаких дополнительных креплений не применялось. Сидения свободно
перемещаются между крайними положениями.
Измеренный объем ящиков составил 7,5 литров.
Много это или мало? Для 6– дюймовых Macrom оказалось: очень мало. Как
выход из тупика пришла мысль: из задней стенки сделать панель
акустического сопротивления. Но до опытов дело не дошло. Решение было
принято такое: применить динамик 25ГДН3–4. Произведены необходимые расчеты
для салона автомобиля с использованием программы JBL Speaker Shop.
Наилучшее акустическое оформление для этих головок – фазоинвертор объемом
7,5 литров с настройкой на частоту 50 Гц. В моей аудиосистеме изначально
предполагалось использовать сабвуферы, поэтому и была выбрана эта частота.
Хотя, если использование сабвуферов не предполагается, частоту настройки
можно взять ниже, реально до 40 Гц. В итоге
был получен тот результат, на который и рассчитывал. Во первых, удалось
разместить "под седлами" ящики минимально приемлемого и максимально
возможного в этом случае объема. Во вторых, это никак не сказалось на
функциональности сидений. В третьих, есть перспективы на базе этих ящиков
сделать более мощную акустическую систему, применив, например, головки
Rocford Fosgate. Эскизы основных деталей
приведены на рис. 4
Рис. 4. Эскизы основных деталей крепления.
Источник: http://tuning-remont.narod.ru/tuning/ak_006.html |